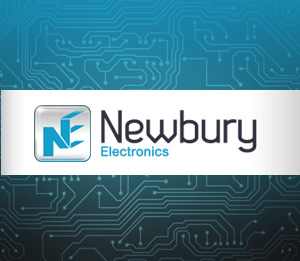
Low cost smd lead-free solder paste reflow
Can you use a cheap domestic oven to re-flow lead-free solder paste? We thought it would be fun to find out. And may be, if it worked, some of you might find our experiment useful.
Our industrial SMD reflow oven is 4 metres long, has 8 convection heated computer controlled temperature zones, and consumes 30Kw of power and only cost £40,000!
An Argos Cookworks Mini Oven, (part number 423/4827) is 50 cms wide, has a 60 minute timer, consumes 1300 watts and costs £39.99.
(Currently in stock at Argos: http://www.argos.co.uk/static/Product/partNumber/4234827/Trail/searchtext%3ECOOKWORKS+MINI+OVEN.htm ).
It’s certainly cheap, being only 1 thousandth of the cost of our industrial oven. Even the cheapest commercial bench-top reflow oven we have seen will set you back around £800.
So you would think an oven costing just £40 should not work, or we would all be out of business.
Read on to find out if it did.
We tested the mini oven like this.
The oven was modified by removing the crumb tray. No other changes were made.
After a few dry run reflow cycles with a temperature profiler to guide us, we homed in towards the correct times and settings.
A test sample based on a 1.6 mm FR4 double sided PCB with 0805 components mounted on lead-free solder paste was made up. This was placed in the centre of the middle tray.
The Cookworks Mini Oven temperature knob was set to 190 C.
The timer was set to 5 minutes and the oven was allowed to heat up.
After 5 minutes, the oven door was opened for 30 seconds.
Then the shelf was slid out to allow the board to cool down a little more.
The completed board was removed and placed on the crumb tray.
A visual inspection showed all the joints were nicely reflowed without any sign of granular paste or solder balling.
So the solder joints looked good. But had we over-cooked the SMD components?
The pcb temperature profile was monitored with a calibrated temperature logger. The red trace on the chart below shows the temperature profile as measured by a thermocouple in free air.
The blue, green and orange traces are the temperatures of thermocouples attached to the pcb.
The heating rate, soak time, time above liquidous, delta t and peak temperature are all within the correct ranges for satisfactory reflow. The components were not overheated.
Our conclusion was that the mini oven worked remarkably well. In fact the temperature profile was far better than expected. Not bad for a £40 oven!
You may be able top repeat our experiment on your workbench. However, we don’t know whether every oven will behave in the same manner. Without a temperature logger, it is not possible to be certain. To ensure components are not fried it is essential to have a temperature log. Our next step will be to build a low cost temperature logger which anyone can construct. In the near future, we hope to be able to offer a ready to go “bare-bones” logger for sale at modest cost.
Watch out for our future blogs about this.