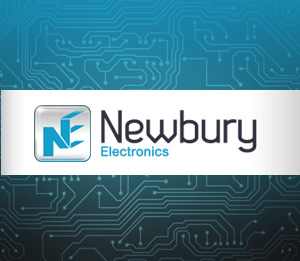
New Nikon XTV 160 X-Ray Machine Reduces our BGA Placement Prices
We have just taken delivery of a Nikon XTV 160 X-ray inspection machine. The machine was only selected after careful consideration of what is available in the market. The device is made in the UK in Hertfordshire, from where, I am pleased to say, large numbers are shipped around the world.
We needed an X-ray particularly for Ball Grid Array (BGA) and Quad Flat-pack No leads (QFN) style component inspection. BGAs have become so large and are mounted so close to the body of the PCB that endoscopic inspection using an Ersascope is impractical. You cannot see far enough down the rows of balls even if the endoscope can be brought to bear avoiding the components that invariably surround the BGA.
So, an X-ray machine is the only realistic option. And given the increasing miniaturization of BGAs, low end X-rays whilst cheap, give such a poor image as to be virtually useless. We will probably only ever buy one X-ray machine for the foreseeable future, so we have selected a very capable machine. The 160 in the machine’s designation represents the anode voltage of the X-ray source, being 160 kilovolts and at the higher end commonly used for PCB inspection. However, the machine will only be operated with the highest power on the densest multi-layer PCBs. The more dense the PCB under inspection (high copper layer count and copper weight for example), the more power that is required to give a useable image.
Power is not the only factor. The X-ray output must be exceptionally stable. The image is generated by detecting very small changes in the amount of X-rays that get transmitted from source to detector. Instability will cause noise, and a poor image. A typical BGA image is shown below.
The XTV160 produces exceptional images because of its nanofocus X-ray spot and advanced image processing. Focus is maintained by a computer controlled electromagnetic lens that ensures the target does not burn even at high kV settings. These features are essential if potential defects are to be identified.
BGA analysis is assisted by true parallel tracking of the images.
When inspecting BGA solder balls, an operator needs to gain a clear view of the ball under inspection. This is normally achieved by combining tilt and rotate movements, and then scanning down the rows ball by ball. The XTV 160V permits this function using a single axis control rather than the usually required three axes. The operator can concentrate on the inspection process and not on guiding the machine.
True concentric imaging makes it easy to rotate the view point round the point of interest. The diagram below illustrates the complexity of the geometry required.
Once an interesting point on the PCB is identified and positioned in the centre of the screen, it remains locked in position no matter what tilt, rotation or magnification is applied. This is a great benefit when inspecting BGA balls.
Excellent resolution and magnification allows superior defect identification. This is a picture of a gold wire bond. These are tiny, and the image below is clear and sharp.
The X-ray source is designed to allow a PCB to be placed within 250 microns of the X-ray focal spot, allowing up to an exceptional x 6000 magnification. The PCB can be viewed at very steep angles enabling clear inspection of solder joints and heat-sinks, maintaining sufficient X-ray energy.
Here are samples of the images and reports available. Special functions are available for inspection of semiconductor package voids, wire bonding and BGA solder bumps.
The picture below shows a PCB assembly ready for inspection. The PCB is shown placed upon the mounting fixture above the X-ray source.
The machine provides a generous 400x400mm (16”x16”) scan area, large enough for most PCB assemblies.
Our machine is complete with X-ray Computed Tomography (x-ray CT) inspection capability. X-ray computed tomography (x-ray CT) uses a computer to re-construct a 3D image from multiple 2D X-ray images of the object taken from a controlled angular rotational scan. Such scans give a clearer graphic display of the object under inspection, and allow the viewer to virtually rotate the 3D image.
Having an in-house X-ray capability decreases our costs of placing BGAs and our price to place these parts has been considerably reduced. If your product requires BGA placements, please check our prices on our online calculator at www.pcbtrain.co.uk.