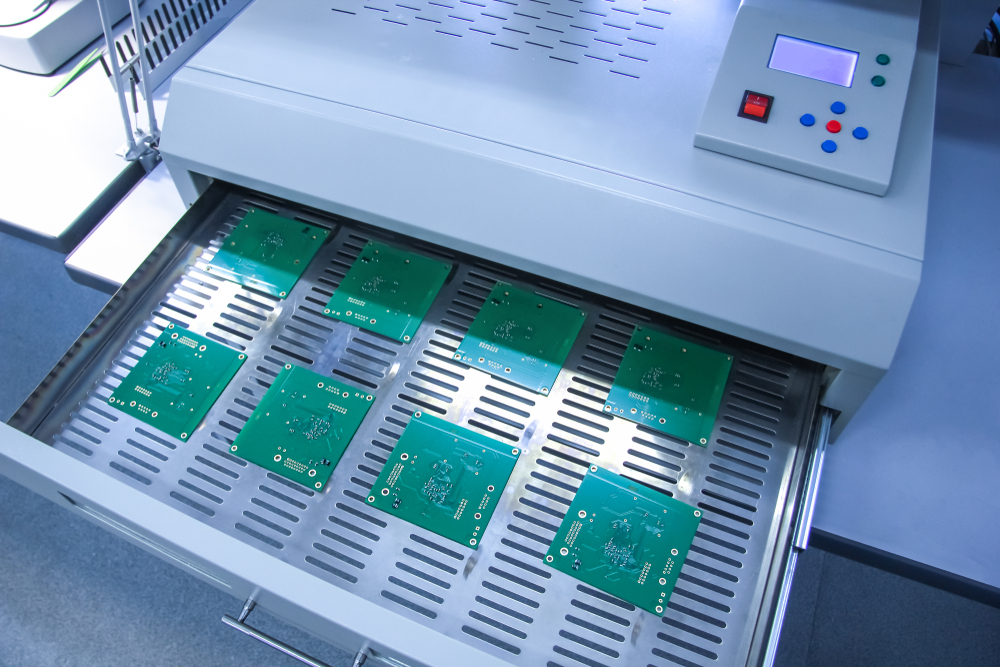
What Is Reflow Soldering?
Printed circuit boards are complex assemblies of substrates, solder and electronic components. They are put together in two ways: reflow soldering or wave soldering. In today’s blog, we’ll take a detailed look at reflow soldering and the role it plays in modern PCB manufacturing.
The use of reflow soldering in surface mount PCB assembly
Reflow soldering is a process in which molten solder attaches electronic components to printed circuit boards. When it reaches its melting point, the solder paste, typically a mix of flux and powdered solder, creates strong and permanent solder joints on the PCB. The solder is usually heated in a specialist piece of equipment known as a reflow oven, which features a conveyor belt for large production runs and multiple temperature-controlled zones.
In recent years, reflow soldering has become the most popular method of attaching surface mount components to PCBs. There are, however, instances where reflow ovens adhere through-hole components to printed circuit boards as well.
Key considerations for solder reflow
There are several stages to reflow soldering, including selecting high-quality materials and ensuring the optimal conditions for your reflow oven. The choices you make here are very important as they will ultimately determine the success of your PCB assembly. Here are some key considerations.
- Pick the right machine: Make sure you have a reflow oven suitable for your requirements. Think about the size of your production run and how often you need to use your machine. There is also a range of different reflow oven designs available. These include models with mesh conveyors or manual width adjustment settings. There are three main types of reflow machine distinguished by the means of heat transfer to the solder paste. These methods are infrared, hot air convection, and vapour phase reflow. Briefly, infrared is fast but it is inherently difficult to control the temperature profile. Hot air convection is fast, and more expensive, but with excellent heat profile control. Vapour phase reflow is a slower batch process, but has superb heat control and is ideal for small runs.
- Create the ideal reflow profile: Everything from the PCB’s material and thickness to the number of layers it has will affect the set-up of your reflow oven. You will also need to consider the number and type of the surface mount components and how these will react to changes in temperature.
- Accurate component placement: Before your PCB enters the reflow oven, all of its components should be in place. You can ensure accurate component placement by using a PCB stencil to apply solder paste to the circuit board and a pick and place machine for more precise component positioning.
What are the stages of the reflow soldering process?
A typical reflow soldering cycle has four steps: preheat, soak, reflow and cooling.
Preheat is the first stage of reflow soldering and consists of heating the components, solder and PCB to a specified temperature. Take care to heat everything gradually to avoid damage or defects.
The thermal soak phase ensures that every part of the circuit board is at the correct temperature. It is here that the flux is activated to reduce the oxidation of leads and pads.
Reflow is the stage where the reflow oven is heated to around 240 degrees Celsius to melt the solder paste. This typically takes 30-60 seconds. Keep an eye on the temperature throughout to minimise component failure.
Cooling is the fourth and final phase. Proper cooling is important as it helps to create secure solder joints and eliminate excess inter-metallic formation or thermal shock.
Which is better, reflow or wave soldering?
In addition to reflow soldering, the other commonly used PCB assembly technique is wave soldering. Typically used to fix through-hole components to PCBs, wave soldering refers to when molten solder moves across a circuit board in a wave-like motion. Unlike reflow soldering, there is no solder on the PCB before wave soldering begins.
So why choose one over the other?
While wave soldering is ideal for bulk PCB assembly of circuits with 100% through hole parts, reflow soldering is geared to circuits with 100% surface mounted parts, giving PCB manufacturers more control over machine conditions, enhancing quality and reliability. In many instances, the latter is also much cheaper, so may be the preferred option for those looking to reduce assembly costs.
You may well be asking, what happens with a circuit which is populated with a mix of leaded and surface mount parts? This is a common eventuality. There are three ways to deal with this. SMD parts can be glued down and soldered at the same time as the leaded parts over a solder wave. The leaded parts can be inserted into pads which have been pre-pasted with solder paste and they can be reflowed along with the SMD parts. Lastly, SMD parts can be reflowed first, and the leaded parts can be selectively wave soldered afterwards. A selective wave soldering machine has a CNC controlled mini-solder wave head which solders each leaded part in turn.
PCB assembly services at Newbury Electronics
Now that you know more about reflow soldering, it's time to get in touch with the experts. Newbury Electronics has 65 years of experience in the PCB industry and proudly uses many advanced assembly techniques to create high-quality printed circuit boards in accordance with your requirements. We use both multi-zone hot air convection and vapour phase reflow ovens according to the requirements of each assembly. Leaded parts are soldered with CNC selective soldering machines.
For more details on what we can do for you, visit our contact page today.